A Comprehensive Guide to the Refine and Benefits of Plastic Extrusion
In the large realm of production, plastic extrusion emerges as a extremely reliable and essential procedure. Transmuting raw plastic right into constant profiles, it provides to a myriad of industries with its amazing adaptability.
Recognizing the Fundamentals of Plastic Extrusion
While it might show up facility initially glance, the procedure of plastic extrusion is essentially straightforward - plastic extrusion. It is a high-volume manufacturing method in which raw plastic is thawed and formed right into a continuous profile. The procedure starts with the feeding of plastic material, in the type of pellets, granules, or powders, right into a heated barrel. The plastic is after that melted making use of a mix of warm and shear, used by a turning screw. Once the molten plastic reaches completion of the barrel, it is required via a small opening understood as a die, forming it into a preferred kind. The shaped plastic is after that cooled down, strengthened, and reduced into preferred lengths, completing the procedure.
The Technical Process of Plastic Extrusion Explained
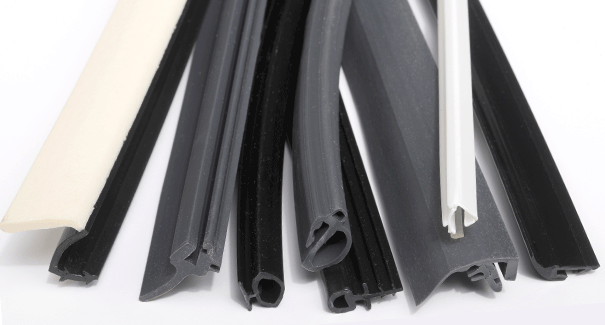
Kinds of Plastic Suitable for Extrusion
The choice of the appropriate sort of plastic is an important facet of the extrusion procedure. Various plastics provide one-of-a-kind residential or commercial properties, making them extra matched to specific applications. Polyethylene, for instance, is typically utilized because of its affordable and simple formability. It provides superb resistance to chemicals and dampness, making it ideal for products like tubes and containers. Polypropylene is one more popular selection due to its high melting factor and resistance to tiredness. For more durable applications, polystyrene and PVC (polyvinyl chloride) are frequently chosen for their toughness and durability. These are typical alternatives, the selection eventually depends on the details demands of the product being produced. Recognizing these plastic types can substantially improve the extrusion procedure.
Comparing Plastic Extrusion to Other Plastic Forming Approaches
Comprehending the types of plastic appropriate for extrusion leads the method for a wider discussion on just how plastic extrusion piles up versus various other plastic forming approaches. Plastic extrusion is unmatched when it comes to producing continual profiles, such as gaskets, seals, and pipelines. It also permits for a consistent cross-section along the length of the product.
Trick Advantages of Plastic Extrusion in Manufacturing
In the realm of production, plastic extrusion supplies several considerable benefits. One noteworthy benefit is the cost-effectiveness of the process, which makes it an economically enticing production method. In addition, this technique provides superior item adaptability and improved production rate, thereby raising overall production performance.
Affordable Manufacturing Method
Plastic extrusion jumps to the leading edge as a cost-effective manufacturing method in manufacturing. This process stands apart for its ability to produce high quantities of product rapidly and effectively, giving producers with considerable financial savings. The key price benefit is the ability to use more economical raw materials. Extrusion makes use of polycarbonate materials, which are less costly contrasted to steels or porcelains. Even more, the extrusion process itself is reasonably easy, minimizing labor prices. In addition, plastic extrusion needs much less power than conventional production techniques, adding to lower functional prices. The procedure additionally lessens waste, as any type of excess or malfunctioning materials can be reused and reused, supplying another layer of cost-effectiveness. important site In general, the financial advantages make plastic extrusion an extremely eye-catching alternative in the production industry.
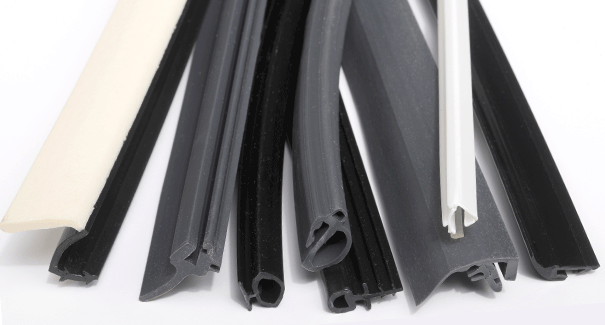
Superior Item Versatility
Beyond the cost-effectiveness of plastic extrusion, an additional significant advantage in producing lies in its superior product flexibility. This makes plastic extrusion a perfect option for industries that require personalized plastic components, such as vehicle, building, and packaging. In significance, plastic extrusion's item flexibility promotes technology while improving functional efficiency.
Enhanced Production Speed
A substantial benefit of plastic extrusion lies in its improved production speed. This production procedure permits for high-volume production in a reasonably brief time span. It is qualified of generating long, continuous plastic profiles, which significantly minimizes the production time. This high-speed manufacturing is particularly beneficial in Discover More Here sectors where big amounts of plastic components are required within tight target dates. Few other manufacturing processes can match the rate of plastic extrusion. In addition, the ability to keep constant high-speed production without compromising product quality sets plastic extrusion aside from other techniques. The enhanced production rate, for that reason, not only enables suppliers to meet high-demand orders however additionally adds to enhanced performance and cost-effectiveness. This useful function of plastic extrusion has actually made it a favored choice in countless industries.
Real-world Applications and Impacts of Plastic Extrusion
In the world of manufacturing, the method of plastic extrusion holds extensive relevance. The economic advantage of plastic extrusion, mainly its high-volume and cost-effective output, has actually reinvented manufacturing. The sector is constantly aiming for developments in recyclable and naturally degradable products, showing a future where the benefits of plastic extrusion can be preserved without jeopardizing ecological anonymous sustainability.
Verdict
In final thought, plastic extrusion is a efficient and extremely effective approach of transforming basic materials into diverse items. It supplies many advantages over various other plastic developing approaches, consisting of cost-effectiveness, high outcome, marginal waste, and layout adaptability. Its effect is profoundly felt in various industries such as building and construction, auto, and consumer items, making it a pivotal procedure in today's manufacturing landscape.
Digging deeper into the technical procedure of plastic extrusion, it begins with the selection of the ideal plastic product. Once cooled down, the plastic is reduced right into the needed lengths or injury onto reels if the product is a plastic movie or sheet - plastic extrusion. Comparing Plastic Extrusion to Various Other Plastic Forming Methods
Comprehending the kinds of plastic appropriate for extrusion paves the means for a more comprehensive conversation on how plastic extrusion stacks up versus various other plastic creating techniques. Couple of various other production processes can match the rate of plastic extrusion.
Comments on “Plastic extrusion for extra-durable, resilient materials”